
Like a moth to a light, I chucked up the bad boy! Went right for the good stuff. The turtle shell looking burl Maple! I made no plan, didn’t have a clue as to form. I’m a lathe turning artist by golly. Simply going to let things happen.
Safety First, I had asked around about turning “wild” type wood. I’ve heard, especially with the spalted woods, you need to be careful about the dust containing molds. Eye and sinus infections could result. So for me, on with a good respirator and eye protection.
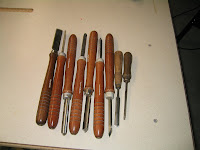
I don’t have the high flautin bowl gouges the “real” turners do. Perhaps if the turning bug bites me hard, some day I’ll join that club. But I do have a set of “Sears Craftsman value pack turner specials” sitting on my bench. And since my chisels look every bit like they were dragged behind a car, (perhaps that is why our previous owner put an eyehook into each chisel handle,) needed sharpening.
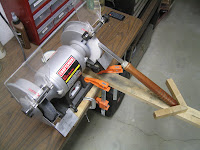
Ok with sharp chisels, were ready to go! Things were going great till a few chunks came flying off, harmless though. Cut into a few soft spots. More worm/insect tunnels to cut through, but ultimately, arriving to a nice cylinder shape, smaller than I was hoping for, but doggoned, I had something to work with.
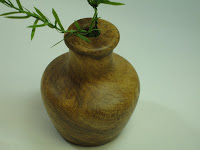
My
Weed Vase, sanded smooth and 5 coats of
General Finishes SEAL-A-CELL Clear. The Maple burl really drank in the oil, so basically keep coating till it won’t take any more.